Sottoponiamo un’interessante case history relativa alla partnership tra l’azienda italiana Fedegari Group, produttrice di impianti equipaggiati di camere autoclave saldate e di sterilizzatori per varie applicazioni industriali e ABB.
La sfida
Il produttore italiano Fedegari Group voleva ridurre i tempi di produzione di autoclavi, destinati all’industria farmaceutica. Le rigorose norme internazionali che impediscono di alterare la velocità o la tensione del processo di saldatura hanno implicato la necessità di migliorare l’efficienza del processo stesso.
Grazie all’introduzione dei robot industriali ABB e dello strumento di programmazione offline RobotStudio, Fedegari Group ha ridotto del 50% i tempi di produzione di componenti autoclavi, specifiche per l’industria farmaceutica.
L’azienda produce impianti equipaggiati di camere autoclave saldate, personalizzati su misura per soddisfare le esigenze specifiche dei loro clienti. Ciò significa che pochissime camere sono uguali e questo richiede un sistema di produzione altamente flessibile, in grado di produrre giunti di precisione e di gestire le dimensioni e le geometrie molto diverse dei componenti autoclave.
Sebbene Fedegari utilizzasse già un sistema robotizzato di un altro produttore, questo era ormai diventato obsoleto e non particolarmente efficiente. Inoltre, alcune operazioni dovevano essere gestite manualmente.
Per soddisfare la crescente domanda da parte delle case farmaceutiche, l’azienda aveva bisogno di accelerare i tempi di produzione. Tuttavia, con i parametri di saldatura fissati dagli standard internazionali, non era possibile ottenere questo risultato modificando aspetti quali la velocità della testa di saldatura o la tensione di saldatura.
L’azienda doveva invece trovare un modo per migliorare l’efficienza complessiva del processo produttivo. Fedegari aveva dunque bisogno di un processo automatizzato in grado di passare rapidamente alla produzione di un nuovo componente con tempi di cambio quasi nulli. Ciò richiedeva non solo robot con la flessibilità necessaria per gestire processi diversi, ma anche un sistema di programmazione offline che potesse modificare un programma pronto per il componente successivo mentre la cella di saldatura lavorava sul prodotto corrente.
Tale sistema avrebbe consentito di creare una libreria di programmi precompilati, adattabili alle esigenze di ogni nuovo componente personalizzato e da inviare alla macchina. Questa programmazione rapida avrebbe permesso di disincentivare i saldatori dal creare manualmente i propri programmi di saldatura posizionando il robot in ogni punto, una pratica che ha causato ritardi.
Oltre a un sistema di programmazione flessibile, Fedegari necessitava anche di una cella altamente adattabile, in grado di accogliere componenti autoclavi di dimensioni diverse e di eseguire tutte le operazioni di saldatura senza la necessità di fermare e spostare le autoclavi.
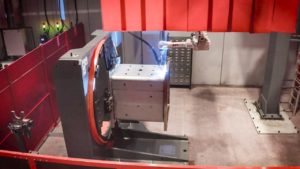
La soluzione
ABB ha fornito due celle di saldatura flessibili basate su robot ABB a portale, insieme allo strumento di programmazione offline RobotStudio per progettare nuove configurazioni e ridurre i tempi di programmazione e cambio.
Le autoclavi sono solitamente dotate di due porte ed è stata una sfida sviluppare una soluzione che garantisse l’esecuzione di tutti i processi di saldatura richiesti senza modifiche. Il processo di produzione prevede la manipolazione di assiemi composti di lamiere piegate e parti ottenute da lavorazioni meccaniche “telai”, costituenti sia della “camera” sia delle porte, con l’utilizzo sia di acciaio inossidabile sia di acciaio al carbonio. Il processo utilizza tre diversi materiali di saldatura e il robot deve cambiare la torcia di saldatura fino a tre volte, a seconda del prodotto da realizzare. È necessario eseguire operazioni di saldatura sia all’interno sia all’esterno della “camera”.
La flessibilità fornita dai robot ha permesso di ottimizzare il progetto finale della cella, coprendo l’83% delle varie dimensioni delle autoclavi disponibili nella gamma di prodotti Fedegari.
Per Fedegari, una caratteristica fondamentale della collaborazione con ABB è stata la sua capacità di agire come general contractor, offrendo la possibilità di trattare con un solo interlocutore.
Attraverso il suo Global Solution Center italiano per la saldatura e il taglio, ABB si è assunta la responsabilità dell’intero progetto, dallo studio concettuale all’avvio della produzione, lavorando in collaborazione con il suo partner system integrator PRSE S.r.l.
ABB ha fornito una soluzione completa per la saldatura robotizzata composta da due celle di saldatura.
L’applicazione
Le due celle possono saldare sia all’interno che all’esterno senza interruzione del ciclo di produzione dei componenti autoclavi, con attrezzature di manipolazione dedicate che consentono di caricare un recipiente mentre il robot lavora su un altro. La programmazione offline con ABB RobotStudio® permette di preparare il lavoro successivo mentre quello corrente è in corso, evitando inutili tempi di inattività.
La prima cella è costituita da un sistema ABB XYZ Gantry per la produzione di “camere” dell’autoclave. È equipaggiata con un robot ABB IRB 2600, tre posizionatori flessibili ABB-PRSE per la saldatura di recipienti di diverse dimensioni e un utensile di saldatura multiprocesso completo di sensori di ricerca e tracciamento.
L’altra cella è progettata per la produzione di “porte” dell’autoclave ed è dotata di un sistema ABB XYZ Gantry, un robot IRB 2600, due posizionatori ABB IRBP 2000 per la saldatura di porte di diverse dimensioni e un utensile di saldatura multi processo.
La programmazione offline è stata condotta utilizzando gli strumenti software ABB RobotStudio offline e Arc Welding Power Pack.